The Reaction Injection Molding (RIM) process is an efficient method for producing large, thin-walled components from thermoset polyurethane (PUR). In the RIM process, polyurethane is processed into compact foam, integral rigid foam and semi-rigid foam, making it ideal for a wide range of applications.
Reaction Injection Molding (RIM)
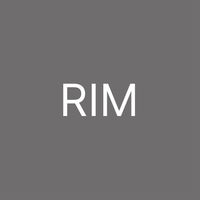
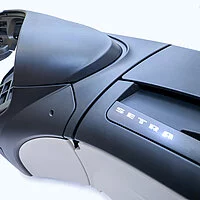
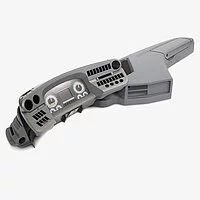
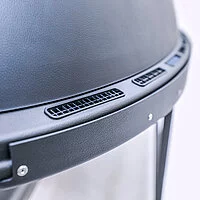
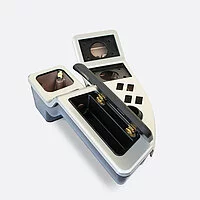
The RIM process
In the RIM process, two components of polyurethane are mixed and the resulting reaction mass is injected into an aluminum tool. The polyurethane undergoes a cross-linking reaction and hardens in the mold, resulting in the finished component. This process is particularly suitable for the production of large, thin-walled components that require high load-bearing capacity, flexibility and resistance.
Materials and areas of application
At C.F. Maier-TEC, we process various polyurethane materials, such as Baydur 30, Baydur 60, Baydur 110 and Bayflex, each of which offers specific properties for different applications:
- Baydur 30: This integral foam is suitable for components with a foil surface, for example made of ABS for robust use or PVC for molded parts with an automotive look. The foil back-foaming enables a particularly hard-wearing surface, ideal for applications with high demands on surface appearance and durability.
- Baydur 60: This material is used to create wall thicknesses ranging from 20 millimetres to almost unlimited thicknesses. It offers a high degree of flexibility in terms of component thickness and is versatile in use.
- Baydur 110: The compact foam Baydur 110 enables a constant wall thickness of up to 5 millimeters. This material is ideal for applications where a constant wall thickness is required.
- Bayflex: Filled with hollow glass beads, Bayflex is characterized by its high flexibility. This material is a high-performance alternative to DCPD and offers excellent mechanical properties combined with low weight.
Advantages of the RIM process
A particular advantage of the RIM process is the ability to easily integrate inserts or adaptation points such as sheet metal angles into the components. Undercuts can also be implemented without any major challenges. The process is suitable for the production of components with different requirements in terms of load-bearing capacity and shape complexity.
After production, the components can be finished with post-processing steps such as priming, painting, printing and EMC coatings (e.g. pad printing or screen printing). Special EMC coatings or antibacterial coatings are also possible in order to meet the specific requirements of the respective application.
Extended variants: RRIM and SRIM
In addition to the classic RIM process, we also offer extended variants such as Reinforced Reaction Injection Molding (RRIM) and Structural Reaction Injection Molding (SRIM):
- RRIM process: Here, a reinforcing material such as glass fibers is added to the polyurethane reaction mass to increase the resistance of the components. This process is particularly suitable for applications that require highly robust components, such as bumpers.
- SRIM process: In the SRIM process, a glass fiber mat inserted in the mould is encapsulated with rigid polyurethane foam. The reinforcing component is completely enclosed by the PUR mass, which further improves the mechanical properties of the components. This method is suitable for applications with particularly high mechanical requirements.
Advantages of Reaction Injection Molding (RIM)
Reaction injection molding (RIM) offers the following advantages:
- Production of large, thin-walled polyurethanecomponents with high load-bearing capacity
- Use of various polyurethane materials (Baydur 30, Baydur 60, Baydur 110, Bayflex) depending on requirements
- Integration of inserts and adaptation points without additional process steps
- Wide range of post-processing options such as painting, printing and special coatings
- Extended RRIM and SRIM variants for increased robustness and better mechanical properties
The RIM process offers a versatile and effective solution for the production of polyurethane components with high load-bearing capacity, flexibility and design freedom. It enables a high level of functional integration and offers numerous options for adapting to specific application requirements.
Would you like to find out more?
Send us an email or use our contact form or use our matchmaker for partnership and cooperation inquiries: