The wet compression molding process is a proven method for manufacturing components made of glass fiber reinforced plastic (GRP ) with a high fiber volume content and smooth surfaces on both sides. This process is particularly suitable for the production of small to medium quantities and offers high product quality and process reliability.
Wet pressing process (NP)
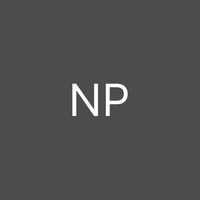
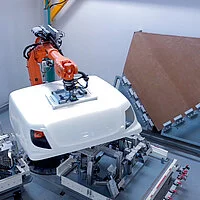
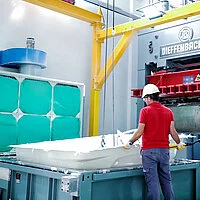
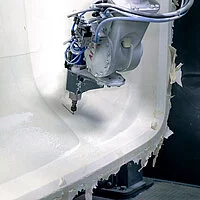
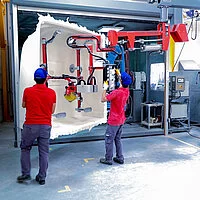
The wet pressing process
In the wet pressing process, a surface gelcoat layer is first injected into a two-part mold to ensure a high level of surface protection and aesthetics. Glass fiber mats are then inserted into the tool and the synthetic resin is poured on using an injection lance. After the mold is closed, the entire mass is pressed and cured under heat. This process produces components with a high fiber volume ratio and high density, as the material is highly compacted during pressing.
Variety of materials and areas of application
At C.F. Maier-TEC, we use both polyester resin and epoxy resin in the wet pressing process, depending on the specific requirements of the application. Polyester resin is preferred for self-supporting constructions and cladding parts, as it is cost-effective and sufficiently stable for most applications. Epoxy resin, on the other hand, is used for higher mechanical requirements as it offers better strength and thermal resistance.
The tools used in the wet pressing process can be made of plastic or metal. Materials such as aluminum, electroformed shells or steel are frequently used. Our plastic tools are manufactured in our own mold shop according to the C.F. Maier standard, which guarantees high process reliability and precision. Post-processing steps such as CNC machining or painting are also carried out directly in-house to ensure consistently high quality.
The wet pressing process is particularly suitable for medium quantities, whereby the components have a higher density compared to the RTM process, as the material is pressed more intensively. However, the process is not suitable for producing cladding parts in Class A quality, as the surface quality is not sufficient. For such applications, we offer alternative processes such as the RTM process or the VEX process.
Advantages and limitations of the wet pressing process
The wet pressing process offers many advantages, particularly in the production of components with a high fiber volume content and smooth surfaces. The high compression of the material results in components with high strength and resilience. The tool costs for plastic tools in mould making are relatively low, which means that the process can also be used economically for smaller annual quantities.
Compared to the RTM process, the wet compression moulding process is characterized by a higher component density, which makes it suitable for applications with high mechanical requirements. However, the production of Class A surfaces is not possible, which is why this process is used more for technical applications than for visible trim parts.
Summary of advantages
The wet molding process offers the following advantages:
- Production of components with a high fiber volume ratio and high strength
- Smooth surfaces on both sides, which are achieved by the closed tool
- Cost-efficient production due to low tool costs in mold construction, particularly suitable for medium quantities
- Use of polyester resin and epoxy resin depending on mechanical requirements
- Post-processing steps such as CNC milling and painting in-house to ensure high quality
The wet pressing process is an efficient method for manufacturing fiber composite components that offers high strength, process reliability and flexibility for medium production volumes.
Would you like to find out more?
Send us an email or use our contact form or use our matchmaker for partnership and cooperation inquiries: