The Sheet Molding Compound (SMC) hot pressing process is an efficient method for manufacturing fiber-reinforced plastics. Pre-mixed compounds of plastic resin and fibers are processed under low pressure to produce components that are characterized by an excellent combination of mechanical properties and surface quality. The process is particularly suitable for the production of large, thin-walled components and enables a wide range of applications in lightweight construction.
SMC hot pressing (SMCHP)
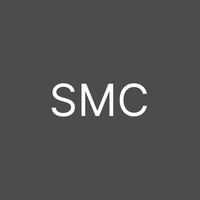
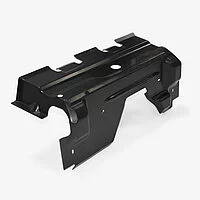
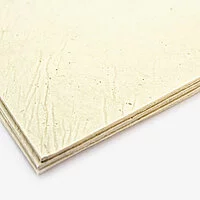
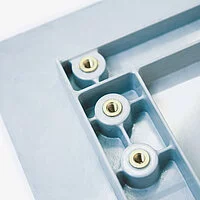
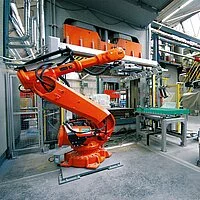
The SMC hot pressing process
The SMC hot pressing process is based on the use of SMC semi-finished products, which consist of a mixture of plastic resin, fiber materials, fillers and hardeners. In the first processing step, the SMC semi-finished product is placed in a pre-heated, two-part mold. There, the material is pressed under low pressure and cured under the influence of heat, resulting in the finished component.
As part of the process, inserts such as fastening elements or threaded bushings can also be inserted directly into the tool and integrated into the components. This ensures a high level of functional integration and enables the precise production of components with complex geometries and inserts. After curing, the components are demoulded and can be further refined by CNC machining or painting.
Materials and areas of application
Fiber-reinforced plastics produced using the SMC hot pressing process offer numerous advantages for lightweight construction. They combine a high-quality surface finish with first-class mechanical properties and are therefore suitable for a wide range of applications, including automotive engineering, rail vehicle construction, boat building, aircraft construction, electrical engineering and sporting goods. Glass fiber-reinforced thermosets play a particularly important role in these areas.
A major advantage of SMC is the variety of possible matrix resins and fiber reinforcements as well as the variable formulation of its other components. Depending on the requirements profile, the basic mixture can be supplemented with additives such as flame-retardant additives or polymers. For example, aluminum hydroxide is added to meet the high fire protection standards in rail transport. The addition of polymer or cellulose fibers can increase the impact strength of the components.
Another advantage of SMC components is their coefficient of thermal expansion, which is similar to that of aluminum or sheet steel. This makes it easier to combine SMC components with steel structures without problems with gap dimensions. These material properties make SMC components an excellent alternative to thermoplastics.
Advantages and properties of SMC hot pressing
SMC hot pressing offers a number of advantages that make the use of this technology in lightweight construction particularly attractive. The most important properties include
- Lightweight construction: SMC components are characterized by a low specific weight, which makes them ideal for use in vehicles and other applications where the focus is on weight reduction.
- High-quality surface finish: The finished components have a smooth surface that can be reworked as required.
- High mechanical strength: SMC offers high strength and stability combined with low weight.
- Weather and chemical resistance: SMC components are insensitive to environmental influences, chemicals and high temperatures, which makes them versatile.
- Wide range of shaping options: Differences in wall thickness, ribs, cams and recesses are easy to realize with the hot pressing process. Fastening elements such as threaded bushes can be inserted directly.
- Cost-effectiveness: The SMC hot pressing process offers relatively short processing times with pressing cycles of just a few minutes. It is a cost-effective solution for medium batch sizes, with quantities ranging from less than 5,000 to 80,000 pieces per year.
Wide range of shaping options
In contrast to flat starting materials such as sheet metal or plastic plates, SMC hot pressing enables flexible adaptation of the shape to technical and design requirements. Differences in wall thickness, ribs, cams and recesses can be easily implemented using press technology. Fastening elements such as threaded bushes can be easily integrated, and wall thicknesses from around 2.5 millimetres can be achieved.
With SMC, engineers and designers therefore have a wide range of options for creating parts that are of high technical quality, economical to produce and attractively shaped with minimal use of materials.
Would you like to find out more?
Send us an email or use our contact form or use our matchmaker for partnership and cooperation inquiries: