The hand laminating process (HL) is a flexible and versatile method for manufacturing components made of glass fiber reinforced plastic (GRP) and other fiber composites. At C.F. Maier-TEC, this process is used in particular for the production of prototypes, custom-made products and small series. By using hand laminating, we meet the specific requirements of our customers and offer a tailor-made fiber composite solution.
Manual laminate process (HL)
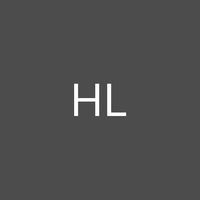
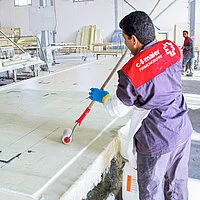
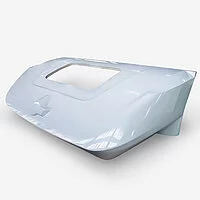
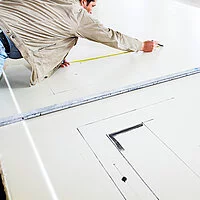
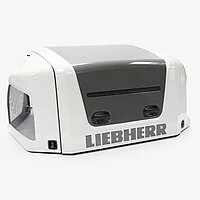
The process of hand lay-up
The hand lay-up process begins with the careful preparation of the negative mold, which is first coated with a release agent to ensure problem-free demolding. A gelcoat layer is then applied to give the component a high-quality, smooth surface finish. The glass fiber mats are then impregnated with synthetic resin in several layers and manually inserted into the prefabricated mould. Repeated lamination and compaction with a special roller effectively removes air pockets to ensure a homogeneous and defect-free structure.
This process is repeated until the desired thickness and strength of the component is achieved. Sandwich constructions can be integrated into the laminate for additional rigidity. Once fully cured, the component is demolded, followed by optional post-processing steps such as CNC milling or painting to ensure optimal quality and fit. The use of cost-efficient single-shell molds from our in-house mold shop contributes significantly to process reliability and helps to reduce overall costs.
Variety of materials and areas of application
Various synthetic resins are used for the production of components using the hand lay-up process, depending on the specific application and requirements. Polyester resin is often used as it is a cost-effective solution for self-supporting structures and cladding parts and meets the requirements of most applications. For more demanding applications that are subject to higher mechanical or thermal loads, we use epoxy resin, which has excellent material properties, including higher strength and better chemical resistance.
The hand laminating process is characterized by a high degree of flexibility and is ideal for the production of prototypes, individual pieces and small batches. This process is also advantageous for larger quantities and special geometric requirements, such as undercuts, as the use of multi-part moulds enables flexible adaptation.
At C.F. Maier-TEC, we manufacture Class A quality cladding parts for buses, trucks, agricultural machinery, construction machinery and caravans. In addition, the hand laminating process is particularly suitable for large-area components such as covers for sewage treatment plants or water basins, which require an exact surface quality.
Advantages and limitations of the hand lay-up process
The hand lay-up process offers exceptional flexibility in the production of components with a wide range of geometries, from simple to highly complex structures. A major advantage is the cost-efficient production through the use of single-shell molds and production in best cost countries, which enables us to offer our customers competitive prices. This process requires well-trained and experienced personnel to ensure consistently high component quality.
For larger series production or specific requirements, such as a particularly smooth B-side, other plastic processing methods may be more suitable. C.F. Maier-TEC offers alternatives such as resin transfer molding (RTM), the vacuum expansion process (VEX) or the wet pressing process. We provide our customers with comprehensive advice on selecting the optimum manufacturing process based on their individual requirements.
Summary of the advantages
The hand laminating process offers the following advantages:
- High flexibility in the production of components with simple to complex geometries
- Cost-efficient production through the use of single-shell molds and production facilities in best cost countries
- Integration of sandwich constructionsfor additional rigidity and stability
- Suitability for the production of prototypes, custom-made products, small series and large-area components
- Production of components in Class A quality for numerous industries, including commercial vehicles, agricultural and construction machinery and caravans
The hand laminating process therefore remains an important manufacturing process for individual and demanding applications where flexibility and high surface quality are crucial.
Would you like to find out more?
Send us an email or use our contact form or use our matchmaker for partnership and cooperation inquiries: